فهرست مطالب
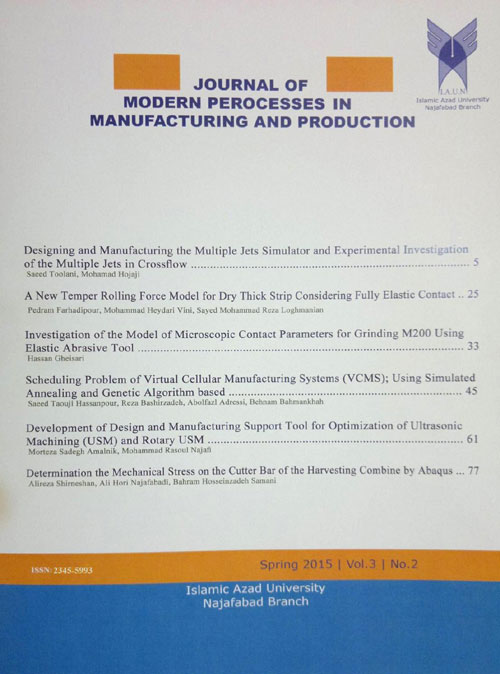
Journal of Modern Processes in Manufacturing and Production
Volume:10 Issue: 4, Autumn 2021
- تاریخ انتشار: 1400/10/20
- تعداد عناوین: 6
-
-
Pages 5-11There is demand for the reduction of friction loss under poor lubricating conditions, for higher contact pressure, and a longer lifetime in internal combustion engines. Overlay technology is one of the effective means for reducing friction loss and improving seizure resistance of journal bearings. The present study describes the fundamental tribological behavior under boundary lubrication of a polyamide-imide (PAI) overlay containing molybdenum disulfide (MoS2) powder. Specimens with different layer structures for the overlay were prepared, and the effects of the layer structure of the overlays were investigated experimentally. As result, the MoS2 in the surface overlay layers became highly aligned through a high-speed spin coating process. In the case of the overlays containing MoS2, the coefficient of friction became almost constantly with a gradual increase, and this was in contrast to the case of the overlays without MoS2.Keywords: Tribology, MoS2, OVERLAY, Composite, solid lubricant
-
Pages 13-25Many advanced robot applications such as assembly and manufacturing require mechanical interaction of the robot manipulator with the environment. Any back-stepping based control strategy proposed for position control of electrical flexible joint robots requires a convergence of internal signals to its desired value called a fictitious control signal. This problem is complicated and time-consuming, whereas a 5th-order nonlinear differential equation describes each joint of the robot. The best idea is to focus on the convergence of main signals while the other signals in the system remain bounded. With this in mind, this paper present a robust Lyapunov-based controller for the flexible joint electrically driven robot (FJER) considering input nonlinearities associated with actuator constraints. It also finds uncertainties associated with robot dynamics. The proposed approach is based on a third-order model instead of a fifth-order model of the robotic system. The stability is guaranteed in the presence of both structured and unstructured uncertainties. The actuator/link position errors asymptotically converge to zero while the other signals are bounded. Simulation results on a 2-DOF electrical robot manipulator effectively verify the efficiency of the proposed strategy.Keywords: Nonlinear robust control, Stability Analysis, Actuator Saturation, Flexible-joint Robots
-
Pages 27-35The cloud manufacturing method is one of the most innovative key enabling technologies for modern manufacturing industry and is claiming increasing attention in manufacturing research. The existing manufacturing models are improved using cloud computing, the Internet of things (IoT), virtualization, service-oriented technologies, and advanced high-speed computing. Cloud manufacturing (CM) aims at a flexible, self-adaptive manufacturing foundation that is capable of dynamically exploiting manufacturing resources and services distributed across the network. As cloud computing is the major enabler for the manufacturing industry, it can transform traditional manufacturing business models into product innovation business models with the help of intelligent factory networks. The service provided by cloud computing for cloud manufacturing, layers, the flow of production service, the layout of production service, and key features is discussed and investigated. Flow criteria in a production service for a typical small, medium enterprise (SME) is introduced. A solution for the security barrier of the CM network is introduced with the help of recent computing technology in this paper.
-
Pages 37-49Over the last several decades, implants have been used to treat fractures and promote healing. The most important reason for deformation and shortening of the bone during healing due to loading on the nails is a lack of strength of the intramedullary nail. Materials with very fine grain dimensions are considered for such purposes. Ultrafine-grained (UFG) materials have structural elements with very fine grain sizes. Several methods for producing UFG materials have been developed, one of which is the top-down approach, which refines coarse-grained metals via severe plastic deformation (SPD). The SPD technique has several advantages that set it apart from other methods of synthesizing. Two of the SPD methods used in this study were the repetitive corrugation and straightening (RCS) process and the equal channel angular pressing (ECAP) process on a 316L stainless steel rod. Mechanical tests were performed on the rods produced using these methods. Under loading, simulation results revealed that the bone implanted by the RCS rod has greater structural stiffness than the bone implanted by an ECAPed 316L stainless steel rod.Keywords: Diaphyseal bone fractures, intramedullary nailing, Severe Plastic Deformation (SPD), Finite elements method
-
Pages 51-59
Material removal modes in brittle material machining are divided into two categories: ductile modes and brittle modes. Many believe that there is a clear difference between energy costs in these two cases. Spindle speed (SS) and feed rate are the effective parameters in the material machining process. It is tried to conduct experimental studies on the effect of low spindle speeds and high feed rates on the turning of brittle material in this paper. Also, the tool geometry is an important factor in turning brittle materials; so the rake angle of the turning tool was changed for dry machining of a single-crystal workpiece. The results show that the surface roughness decreases by increasing the spindle speed and decreasing the feed rate, which reduces the surface damage significantly. The purpose of this experimental study is to investigate the effect of rotational speed and feed rate on surface roughness and surface texture in the lathe process of the workpiece using the ductile mode of machining and changes in the parameters of this process to control the configuration and dimensions of microstructures (micro craters, Surface pits, and micro-cracks).
Keywords: Machining, Spindle Speed, Feed Rate, Rake Angle, Surface Damage -
Pages 61-77
In recent years, there has been a demand for the production of materials with high thermal resistance and manufacturing structures with high mechanical strength in modern industries. In this paper, the frequency responses analysis of the sandwich beams with functionally graded core and homogeneous face sheets are presented based on the high-order sandwich beam theory. All materials are temperature dependent and the properties of FGM are varied gradually by a power-law rule which is modified by considering even and uneven porosity distributions across the thickness. Nonlinear Lagrange strain and thermal stresses of the face sheets and in-plane strain and transverse flexibility of the core are considered. Governing equations of the motion are obtained based on Hamilton’s principle and solved by a Galerkin method for the clamped-free boundary condition. To verify the results of this study, they compared with special cases of the literature. Based on the numerical results, it is concluded that by increasing the temperature, power-law index, length, thickness, porosity volume fraction the fundamental frequency parameter decreases, and increasing the wave number causes the frequency increases.
Keywords: Sandwich Beam, FG Core, Porosity, Temperature-dependent, Clamped-free